For gasses and liquids, a molecular sieve is an excellent absorber. Activating molecular sieves with a distinct design aids numerous systems in effectively removing undesirable gas or liquid contaminants. It can also separate gasses or liquids into molecular size groups. In the distillation of ethanol above the azeotropic threshold of 95.6 percent volume, the molecular sieve plays a significant part. With the use of synthetic molecular sieves, the ethanol dehydration procedure may now be conducted with improved technology further than this azeotropic limit.
We are going to work through the detailed analysis of the designs of the molecular sieve adsorbent bed for ethanol dehydration. Let’s get to it!
The Use of Molecular Sieve Bed in Ethanol Dehydration
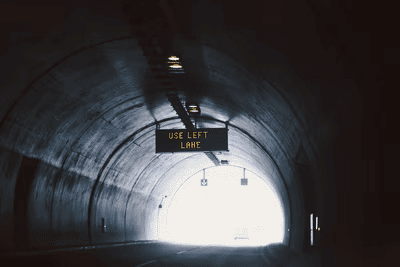
What is a Molecular Sieve Bed?
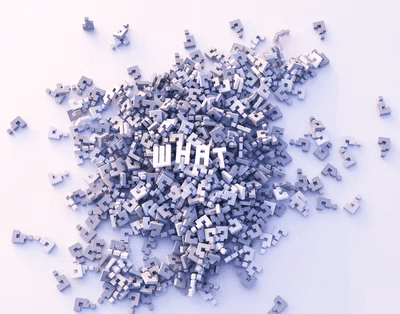
The Artificial zeolite substances holes of exact and homogeneous design and size are known as molecular sieves. This enables them to adsorb gasses and liquids based on molecule size and permeability preferences. Zeolites are highly permeable crystalline solids that are found in nature and belong to the aluminosilicate chemical family.
3A, 4A, 5A, and 13X are the four major classifications of molecular sieves. The molecular sieve’s pore dimension is determined by the type, which is determined by the synthetic version of the molecule. A molecular sieve operates by solubilizing gas or liquid molecules tinier than the functional diameter of its pores and rejecting molecules larger than the holes.
What is the Function of Molecular Sieve in Ethanol Dehydration?
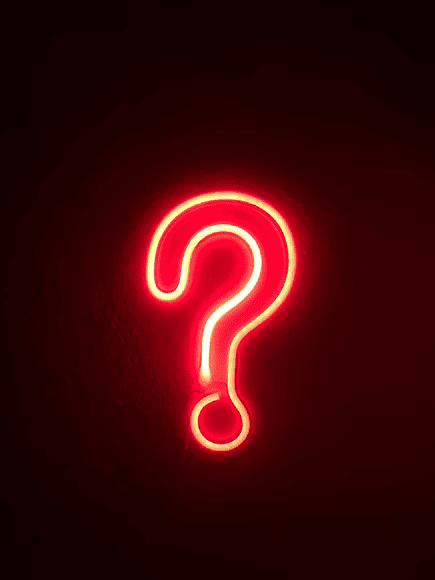
Conventional ethanol distillation can only attain a purity of about 96 percent ethanol, with the residual 4 percent being water, due to the azeotrope generated when it is combined with water. To be deemed fuel quality, ethanol must be dehydrated to at least 99.9%. A 3A molecular sieve, constructed specifically with 3 Angstrom-sized openings, is utilized to adsorb the water molecules, whereas the bigger ethanol molecules are rejected, to attain this degree of purity. This procedure efficiently dehydrates ethanol to the necessary level of purity so that it can be called fuel grade because there is no rivalry for sorption.
During the production procedure, the diameter of the pores in both particles of molecular sieves is carefully monitored. To control the size of the pore aperture, sodium, calcium, and potassium ions can be exchanged within the particles. This enables gas and liquid molecules to adsorb preferentially. Consider a parking garage: your vehicle is 7 feet tall, but the garage roofing is only 6’8 inches tall. You will not be able to get your car into the garage, no matter how hard you try. The adsorption of particles in the openings of a molecular sieve works on the same principle.
Common Types of Molecular Sieve Used for Ethanol Dehydration
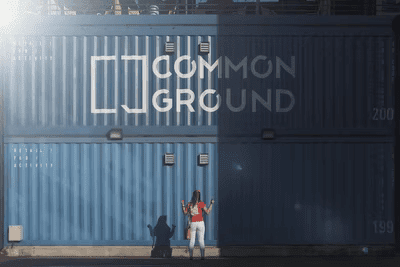
In a variety of commercial and food uses, the Molecular Sieve Dehydration Procedure necessitates a high degree of purity. The most effective type of molecular sieve for drying ethanol is Type 3A. The hydrated ethanol vapour is routed via the molecular sieve bed during the ethanol dehydration procedure. Water is absorbed by the pores of the adsorbent design as the vapours travel through the sieve bed in the initial step. The adsorption procedure continues until the vapours’ probable water adsorption is accomplished or the molecular sieve is saturated.
The water is transferred from moist ethanol vapour to the activated molecular sieve via an area or region where the moisture content is reduced from input to outflow. This master transition zone has one active bed for dehydration transit and another for regeneration. Employing powerful gates and automation, the motion from one bed to the next is handled and managed. Pure ethanol can be applied as a fuel in automotive and other uses once it has been dehydrated using molecular sieves.
How Much Molecular Sieve Should You Use
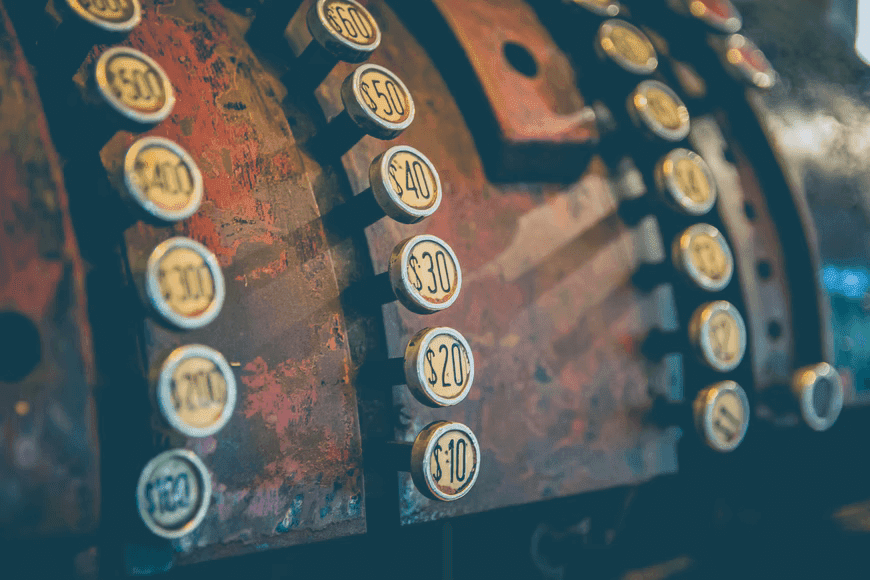
The drying ability of molecular sieves is around 20% to 25% of their own mass. For the dehydration procedure, pour molecular sieves equal to 3 to 4 times the anticipated amount of organic solvent, and swirl it occasionally for around 24 hours.
The Most Effective Design of Molecular Sieve Bed for Ethanol Dehydration
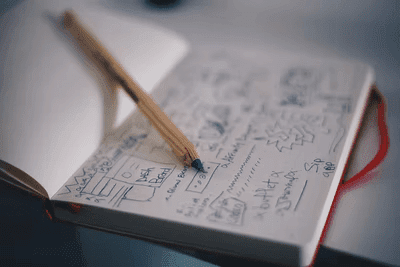
The design and function of a molecular sieve mechanism are influenced by a number of factors. The adsorption capacity of a contaminant is determined by its functional temp and partial pressure, as well as the kind of molecular sieve (3A, 4A, 5A, 13X). Flowrate and pressure decrease limitations, in combination with adsorption volume, are critical in determining the best flow pattern, weight transference kinetics, and, by appendage, container design.
The size of containers is also influenced by the pore dimension of the molecular sieve, as well as the bed arrangement (depending on adsorbent thickness and composed of giant granules, small granules, or a split bed). The pressure decrease and flow dispersion, as well as the regeneration activity needs, will be influenced by the diameter-to-height ratio chosen.
There are two design possibilities for the dehydration component: integrated or stand-alone designs, based on the parameters of hydrous ethanol feedstock and the availability of an alcohol distilling facility.
1. Integrated Design
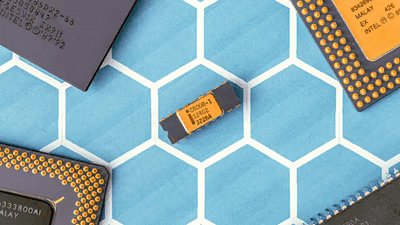
Integrated vaporous feed dehydration machines are connected to a distillation system and accept hydrous ethanol vapour straight from the rectifying tower. The regeneration flow, also known as the purge stream, is reintroduced to the distillation for ethanol recuperation.
When contrasted to uncoupled units, the most significant benefit of the integrated system is a significant reduction in energy usage. Vogelbusch’s innovative power-effective heat integration of dryness with distillation/rectification/evaporation systems substantially reduces operating expenses.
The least pressure of 0.5 barg is required for feeding.
2. Stand-Alone Design
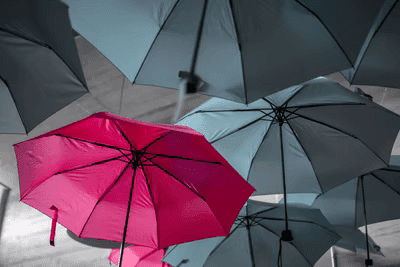
Hydrous ethanol liquid from stockpiling is dried using stand-alone liquid feed drying equipment. In a tiny recycling column, the hydrous ethanol is evaporated. The regeneration channel, also known as the purge stream, is routed to the recycle chamber for ethanol extraction.
An appropriate design of heat recovery, taking into account feedstock and utility parameters reduces the power consumption of the ethanol drying chamber.
The Principle of the Procedure
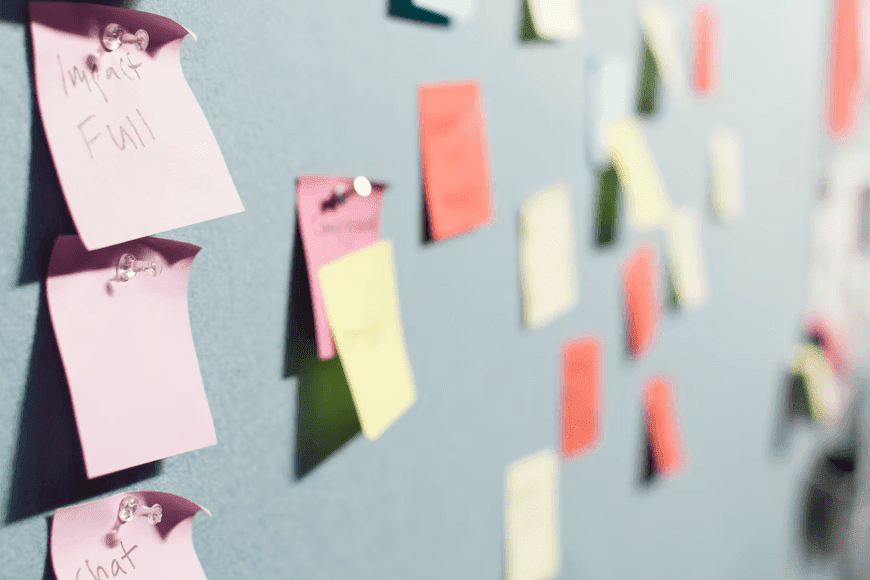
The adsorption technique used in molecular sieve dehydration uses synthetic zeolite, a brittle, high porosity substance. The method is based on the fact that the attraction of zeolite for water switches with pressure. The zeolite’s water packing is determined by the partial pressure of the water in the input, which may be changed by changing the force.
The Pressure Swing Adsorption Procedure(PSA)
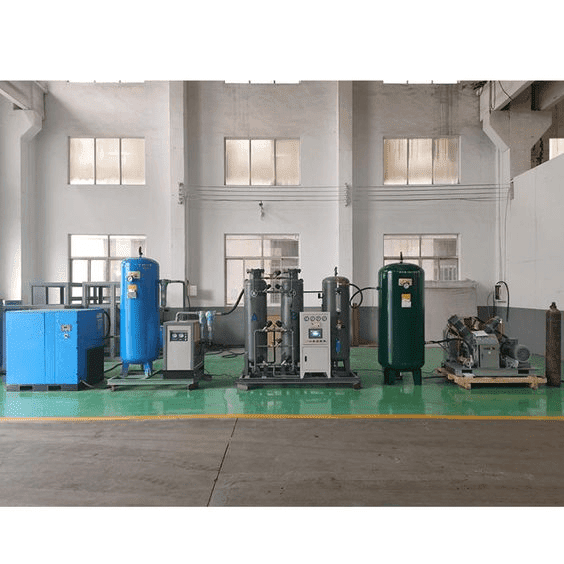
No condensation occurs because the molecular sieve bed is injected with superheated vapour. Ethanol vapour flows via the bed while vapour is absorbed into the openings of the zeolite.
When the molecular sieve bed becomes drenched with water and a breach is near, it must be reactivated: the water is removed from the surface of the zeolite by lowering the pressure exerted on it.
A pressure swing adsorption setup with two molecular sieve beds is used to achieve constant production. One bed is in the process of being dehydrated, while the other is being regenerated beneath a vacuum. Bed pressure is reduced throughout the activation, and the desorbed water is whisked out of the bed along with output vapours from the other drying bed. This purging or regeneration channel is then deliquesced and pumped to the distillery for ethanol extraction.
The entire procedure is automated.
How to Make Dehydration Units Work Better
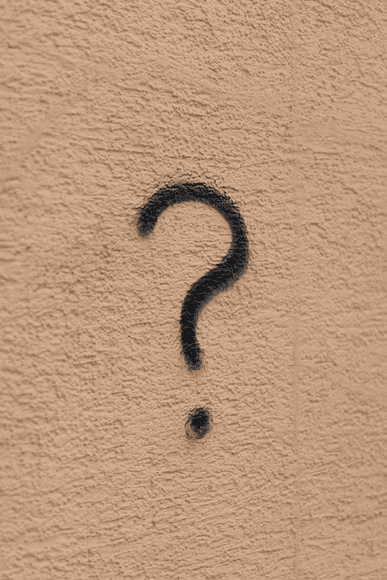
Enhancement of the Molecular Sieve Procedure
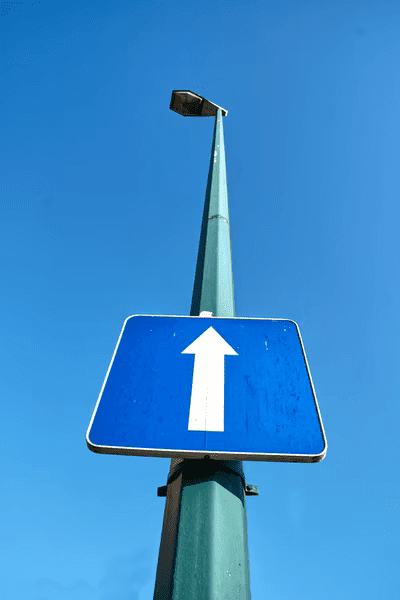
- Adsorption Optimization Principle One: Ideal Temp and Pressure
The inevitable point, based on two main basic rules of adsorption, is that the unit should be operated at the maximum pressure and minimal most temperature feasible. When selecting a temperature for the function, keep in mind that this is a vapour stage procedure, which means the feed channel can’t change stages at any point. As a result, the lowest temperature that can be used is just above the juncture of a stage change. The maximum pressure that the system can bear as well as the quantity of superheat accessible limit the mechanism.
The maximal pressure is determined by the container, pipe, and gate ratings. The boiling point of the ethanol/water solution determines the minimal temperature. The majority of designs are based on the water/ethanol azeotrope, which contains around 95% ethanol. In reality, most plants operate below the azeotrope, with ethanol levels as low as 90%. The true boiling point of any combination must be ascertained. The inlet vapour temp should be set at 50°F or 10°C of superheat to guarantee that the substance remains in the vapour stage.
The perfect parameters for maximal adsorption can be pinpointed by evaluating these factors.
Compute the maximal settings for regeneration using the same isotherm approach. You must achieve the greatest vacuum attainable in the container at a fixed temp. The working capacity is defined as the distinction in capacity at a fixed temperature between the highest pressure feasible possible and the lowest pressure conceivably attainable.
- Adsorption Optimization Principle Two: Working Capacity
A specs sheet must come with every molecular sieve, and it should state the static water capacity. Because all bonded 3A sieve beads have a static capacity of 18-22 percent water by mass, this has a minute bearing on the real working capacity.
The fixed volume of the molecular sieve is useful as a general indicator of its purity, but the functioning capacity is the most necessary for performance. The differential in the water volume of the molecular sieve at a fixed temperature between the twin operating pressures, sorption and activation is described as working capacity.
The mass transference zone is the region where water is consciously adsorbed or eluted from the molecular sieve throughout an adsorption or regeneration phase of the loops. Hypothetically, the mass exchange zone is shaped like a “plug flow,” a spherical wafer that travels uniformly throughout the diameter of the bed. In actuality, both the vapour dispersion and the friction on the container’s walls form the mass transfer region. To achieve full use of the molecular sieve output, proper dispersion is essential for appropriate vapour dispersal.
Factors that Influence Working Capacity
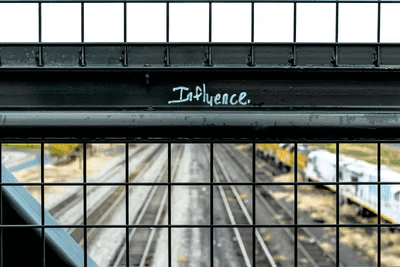
- Under the specified constitution and pressure, temp must constantly assure vapour stage maintenance. Since the liquid creates an obstacle on the bead exterior, mass transference of the liquid into the crystal junction is hampered in two-phase circulation. The liquid’s surface tension proves it hard to eliminate the liquid water through re-vaporization after it has compacted to the liquid stage.
- Vapor dispersion at the intake. Symmetry and velocity of the mass transference zone.
- Ensure maximum disparity between the adsorbent pressure and the regeneration suction at a fixed temperature.
- The appropriate size of 3A molecular sieve.
- Ask for sample Certificates of Assessment in addition to specs sheets. Evaluate molecular sieve products from different producers; they aren’t all made the same and thus don’t perform the same. Check for attributes such as Crush strengths, wear abilities, the dimensions of the particles they are distributing, and technical knowledge.
What Else to Consider
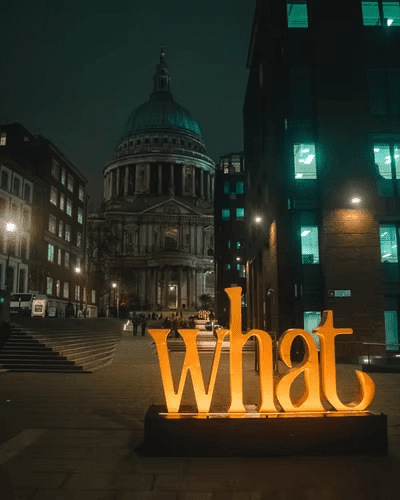
The corporate ethanol production procedure relies heavily on molecular sieves. They enable ethanol to be dried from 95% purity to approximately 99.9% purity, which is required for usage as a fuel additive. The molecular sieve in ethanol dehydration plants, like all other operations in an ethanol factory, requires special attention. Preventive upkeep, care during the working procedure, and knowledge of what can cause protracted harm to the beads and container, or sheet are all essential. To guarantee a long, sustainable lifespan of up to ten years, proactive monitoring and maintenance of sieve beads are required.
Knowing how molecular sieve beads dehydrate and following a few simple guidelines will help them last longer. With that in mind, observe the following:
1. Avoid wetting the Sheet/Bed
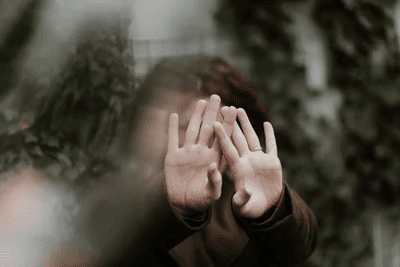
When running into the container and during functioning, caution should be taken to guarantee that the procedure stream arrives and stays in the vapour stage. If the vapour condenses back to liquid, it can have a significant impact on the mass transference dynamics of water into and out of the container, resulting in decreased working capacity and potential destruction to the beads. Due to the obvious cohesive qualities of water, when a liquid-stage process stream reaches an ethanol dehydration bed, water can create a layer over each bead, effectively layering it in liquefied water. The adsorption of vapour stage contaminants (water) from the intended, pure ethanol product stream is slowed or fully prevented by beads covered in liquid water.
It is necessary to accomplish and preserve a feed stream at maximum pressure with 50 °F of superheat—50 degrees Fahrenheit above the condensation temperature—to avoid the appearance of liquid stage molecules during any stage of the dehydration procedure. The ideal superheat temperature is 50 ° Fahrenheit, which is high enough to prevent vapour from reverting to the liquid stage while retaining low enough to not considerably diminish the sieve beads’ operating capacity inside the container. Working capacity is proportional to operational temp; beads under high heat have a lower operation capacity, therefore too much heat throughout the operation is also undesirable. It’s also crucial to have properly insulated containers and pipes to prevent cold zones or uncontrolled temperature variations in the feed stream, particularly during the harsh colder months.
2. Avoid Exceeding Critical Velocity
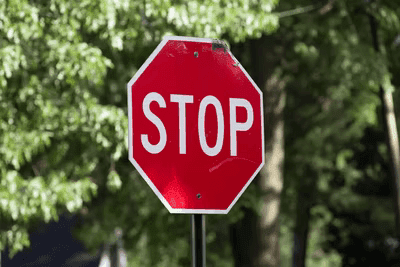
To protect dehydration units and the sieve beads within, critical velocity must be avoided. Each piece of machinery in a process has a maximum pressure that it can withstand without inflicting harm. When a plant’s vapour rate is excessively high, vapour velocity can surpass critical velocity thresholds, resulting in a sound that sounds like screaming or high-pitched wheezing. When critical velocity is surpassed, beads can shatter and break, resulting in extra dust, the enhanced requirement for peripheral unit top-offs, and jeopardization of general working capacity, and may finally necessitate a complete change-out to reestablish productivity.
3. The Bed Shouldn’t Be Bounced
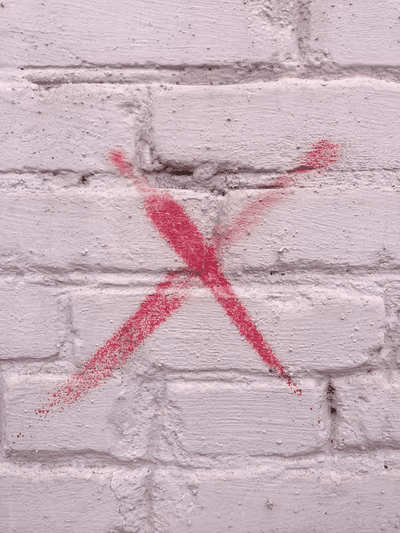
To prevent Levi’s expansion, appropriate velocity regulation within the bed must be closely maintained to guarantee that the fluidization velocity is not surpassed, as defined by each individual system. Bead diameter, flow rate, vapour density, container pressure, and input stream temp all affect fluidization speed. When the beads are elevated and hang in the air on a foam of vapour, a procedure known as fluidization, Levi’s expansion happens. When the beads are fluidized, they might grind against each other, causing significant wear, dusting, and breaking.
As a result, shattered beads can cause the weight transfer region to stream through the bed, resulting in an irregular, early breakthrough, a bad feedback spiral, and recurrent destruction. Immediate fluidization, or the actual bouncing of sieve beads within the container, can be induced by fast changes in pressure triggered by stuck valves or inappropriate pressurization of the container. This is frequently known as popcorning.
If you want to learn more about the capabilities of different ethanol dehydration units, talk to a sieve expert, like those from our company, Jalon. They’ll help you figure out things you initially didn’t know about molecular sieve and essentially save you from making any mistakes. Check valves for appropriate function on a regular basis, arrange team workshops, promote continued education on appropriate pressurizing settings, and emphasize the advantages of regular checks to boost effectiveness and success.
4. Circumvent Pollution
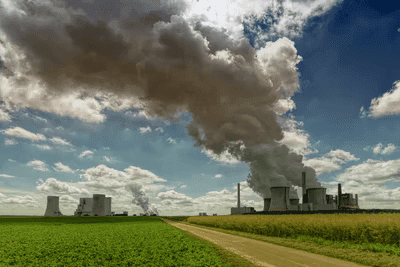
Low molecular weight carbohydrates, such as water-soluble glucose, and fusel oils, can alter the operating capacity of ethanol dehydration units significantly. Carbohydrates are derived from water-soluble glucose that stays in the procedure stream, including other pollutants, as micellar combinations that are then transferred into the beds. In a procedure known as coking, these pollutants adhere to the exterior of molecular sieve beads, forming a coating of coke, or burnt carbohydrates.
Coke appears as dark patches on the surface of the beads and can eventually form a full layer around the surface, rendering the beads black. The coating of coke blocks vapours from accessing the micro-channels within each bead, preventing water from being absorbed by the molecular sieve grains, resulting in a significant reduction in working performance and effectiveness.
Installing demister pads or coalescing separators between the vaporizer and the dehydration unit is the simplest way to reduce hydrocarbons—glucose, fuels, and other impurities. These filters are basically steel wool sheets that catch pollutants and purify the vapour stream as it goes past. To greatly limit the incidence of coke and retain the operating capacity and weight transference rate inside the containers, proactive maintenance crews must inspect the drain on the base of the filter and repair it as required after installation.
5. Be Observant to the pH Level
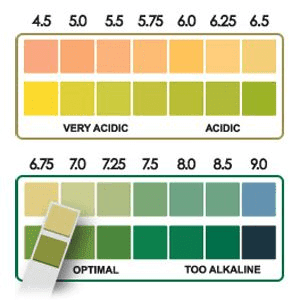
A three-angstrom molecular sieve(3A Molecular Sieve) is developed particularly to dehydrate ethanol and has crystal pore holes measuring roughly three angstroms in diameter. Considering water molecules are approximately 2.8 angstroms in diameter and ethanol molecules are about 3.6 angstroms in diameter, this sieve is suitable for ethanol synthesis. Water molecules can pass through 3A crystals and be entrapped, but ethanol molecules are too big to adsorb and bounce off.
When molecular sieve beads are subjected to a high pH, an ion exchange occurs, converting 3A sieve crystals to 4A or bigger sieve crystals, permitting ethanol molecules to be adsorbed beside the water and reducing capacity.
Sieve beads will disintegrate and agglomerate if subjected to a feed stream with a pH that is too low. To avoid ion transfers or bead fusion, an optimal feed stream must have a pH of 4.5 to 9.0. Technicians must pay additional attention during preventative maintenance to guarantee that clean-in-place chemicals like sulfuric acid or caustic soda (sodium hydroxide) are fully rinsed off and not permitted to pass through the sieve containers.
The Bottom Line
Molecular sieve stands at the centre of most manufacturing procedures and plays a vital role in enhancing the purity of most manufacturing outputs, ethanol included as seen in this post. While the effectiveness of the molecular sieve used matters, you need to keep in mind the quality as well. There are many providers in the market, but only Jalon ensures that you get quality for what you pay for. Contact us and we will be more than happy to supply the highest quality of the molecular sieve. We are able to deliver on both short-term and long-term demands, so you do not have to worry about the timing. And more significantly, we ship our products globally.